‘Not all locks are created equal!’
When it comes to choosing the right safety padlock for your establishment, business sector, lockout procedure and process. There are several areas to consider so that you can choose, utilize and implement them effectively and safely.
The locks themselves form an integral part a safety procedure, however, the wrong lock choices could unravel even the most comprehensive procedure.
Let’s look at when and where locks are used:
- When an operative is to isolate machinery for maintenance, cleaning, inspection and/or business needs.
- An authorised operative is implementing and managing a complex isolation for contractors/staff to carry out works.
- A hasp and/or group lock box is in use and operatives lock the machines out AND the hasp/lock box to manage their own safety.
- When locks are in use for shutdowns where several locks are in situ.
Why do we use them?
- To comply with regulations.
- To ensure nobody else can re-energize the machinery whilst you are compromised.
- To guarantee your own safety.
- To safely manage each step of the process effectively.
Lockout procedures have been implemented across a wide range of industries, sectors and applications. However, we still see regular accidents, resulting in injuries and worse. Below explores how incorrect locks can play their part in this and how the correct safety padlocks can help improve.
Scenario:
‘You purchase 50 safety locks off the shelf in packs of 10. They are guaranteed to be unique to one another per pack, meaning lock number 1 cannot open lock number 2, 2 cannot open 3 and so on. A complex isolation takes place on site and 30 locks are in use, due to the way these locks are manufactured and sold. There is ZERO guarantee that each pack that was purchased, are unique to one another. In effect, this could mean that each 10 locks could duplicate the next. Massively compromising the lockouts effectiveness.
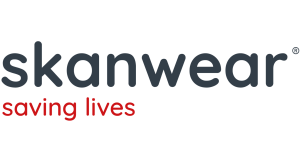
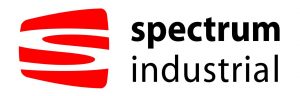
‘Additional to this, its highly common for locks of this nature, to have the key head engraved with the key number, but not the lock. Meaning that if you happen to have 30 locks in situ and duplicates are present. When you come to remove them, it’s impossible to match key to lock. Potentially removing the incorrect lock and re-energizing a machine still being cleaned or repaired. There are some recent UK cases where this exact scenario resulted in a recorded near miss and another with a major injury!
What to Consider:
- Does the lock AND key have the key number stamped as standard?
- Does the safety supplier record each lock number for the site/group automatically? (This method protects duplicate locks being sent on separate invoices – guaranteeing unique key numbers for the lifetime of supply. Its rare companies do this).
- Do the locks use keys that are cut from blanks? (an important factor as some lockout locks on the market, can be cut through a machine, defeating the locks object.
- It’s also important to only receive 1 key per lock and not 2. A newly recognised standard.
More common factors and Issues to consider when deciding which lock to purchase:
Key Systems:
When finalizing the company procedures and lockout processes, it will be evident which keying system will enhance the solution. The below explains each system and how to utilize to help with this:
Keyed Alike:
Keyed alike is a method where ALL locks and keys duplicate one another. This is generally used by companies who use an authorised person to isolate the machine/s for operative or contractors alike. They can also be used as suites, small and large to control safe procedures. I.e. an individual could have 3 locks personally all keyed alike, but this would then differ from the next 3 for another individual. Ensuring the personal safety and unique from one another.
Keyed to Differ:
Keyed to differ, is ensuring that each lock is unique from one another. Consider that locks are not all created equal. Some locks could have very few unique key possibilities, they could have been manufactured using a standard key cut and not a specific safety blank which cannot be replicated/copied. The way they are sold could also be misleading, they can be a pack of 10 locks all guaranteed unique from one another, but the very next pack could duplicate the first.
Ensure to use a supplier who guarantees the unique keyed to differ numbers, who use blanks for them and who record the numbers to manage the supply of locks are always unique even over different orders at different times.
Master and Differ:
Master and differ combine the two above keying systems. Allowing each individual and operative, a uniquely keyed lock. With a master key for either the whole suite of locks or segmenting them into multiple suites. For example, you could have 4 suites of locks, with a master key managing each suite. Suite A Master Key can only open suite A and cannot open B, B cannot open C and so on. This is generally used in an emergency or due to a procedure which renders this the safety process when isolating.
Material Choices:
Depending on your industry, business, environment and outlined safety requirements. The material type you opt for on your locks should be considered. For example, a high risk ATEX area, should look to deploy None-Conductive padlocks which consist or a nylon body AND a nylon shackle, avoiding a spark risk if dropped on plant.
Plastic/Nylon:
The plastic bodies give several benefits, one of the main aspects being they can be colour coded to segment different suites, departments and allocations. They are also lighter than most locks if you are to have more than one on your person. They can be easily etched to further unique the locks and manage/house them correctly. A red safety padlock has quickly become a standard in most industry and a staple padlock choice for most Lockout Tagout Procedures.
Brass:
Brass locks have been the standard in Lockout Tagout from the beginning and are still one of the highest used padlocks in the country. They have been standardised across a number of sectors; many power plants use them exclusively. They can be colour coded, engraved and uniquely keyed as the plastic nylon ones are. They can be more expensive than others, however, they do offer some great benefits such as rust free. Meaning they are used in harsh environments for long periods of time.
To most, Safety Padlocks can be bought with good intentions. However, without considering the safety elements listed above (which may not be made obvious at the time), the locks could diminish and unravel the company lockout procedure, with potentially dangerous consequences.
LOTO Top Tips
- 1 – Clearly identify padlocks and tags either personally or departmentally.
- 2 – Allow time & apply actions to relieve any stored/residual energies.
- 3 – Ensure Lockout equipment is suitable for the intended task.
- 4 – Develop a written programme, with process & procedures with all details that MUST be followed.
- 5 – Any new machines must have a written programme/procedure developed against it.
- 6 – All new & existing staff are to be trained and made aware of LOTOTO, it’s dangers and how to implement safely. According to the standard operating procedure (ongoing activity).
- 7 – The only person to remove a lock is the one who applied it.
- 8 – Implement and review the Lockout Tagout process and procedures annually. Update and improve where required.
- 9 – You must Try-Out every time. Confirming the success of the isolation before proceeding with the task.
Thought of the day.
Lockout Tagout is NOT an optional activity!